JLR Annouces $669.6M Investment to Produce EVs Alongside ICE at Halewood
On September 26, 2024, Jaguar Land Rover (JLR) announced a £500 million ($669.6 million) investment to transform its historic Halewood facility, preparing it for the parallel production of electric vehicles (EVs) alongside existing combustion and hybrid models. Originally built in 1963 to manufacture the Ford Anglia, the Halewood plant is being modernized for the electric era.
With £250 million already invested, the transformation has so far involved over one million hours of construction over the past 12 months. The site has been expanded by 32,364 square meters to accommodate the production of JLR’s medium-sized electric luxury SUVs, which will be built on the new Electric Modular Architecture (EMA) platform.
The historic plant has been equipped with cutting-edge technology, including new EV production lines, 750 autonomous robots, ADAS calibration rigs, laser alignment technology for precise part fitment, and the latest cloud-based digital plant management systems. These upgrades are part of JLR’s vision of creating a “factory of the future” at Halewood, positioning it at the forefront of automotive manufacturing in the electric age.
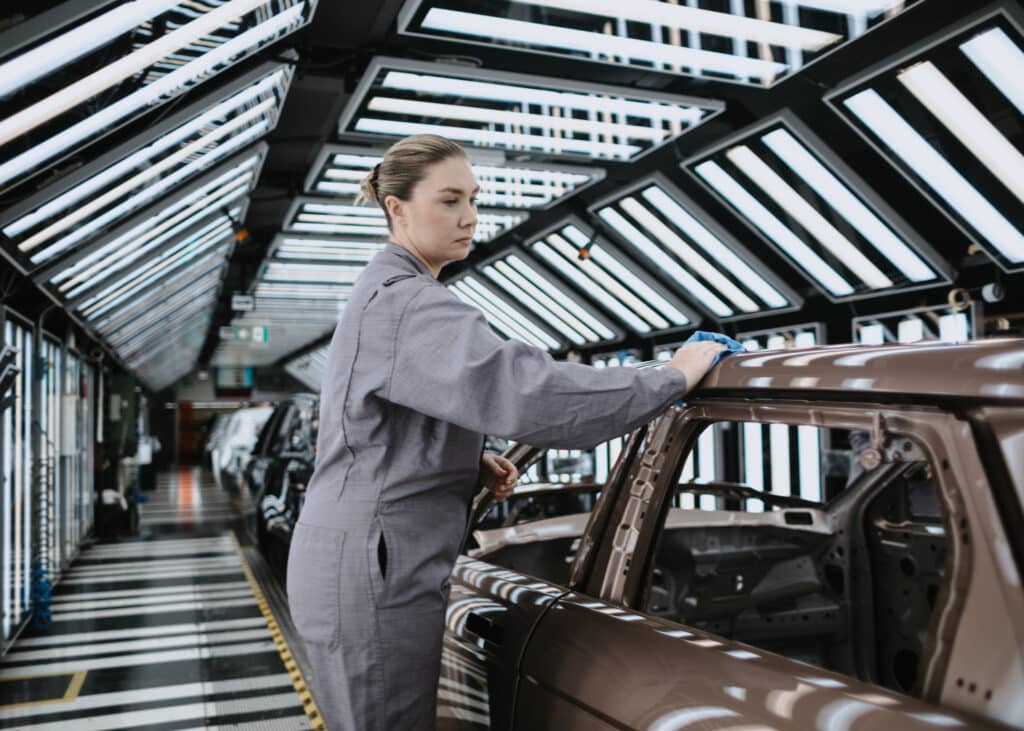
This investment is a key element of JLR’s commitment to its Reimagine strategy, which aims to electrify all its brands by 2030, with a goal of achieving carbon net zero across its supply chain, products, and operations by 2039. Electrification is at the core of this strategy, positioning JLR to lead in sustainable luxury automotive manufacturing.
The Halewood facility plays a vital role in this transformation, with an exciting future ahead. Initially, it will produce internal combustion engine (ICE), plug-in hybrid (PHEV), and battery electric vehicle (BEV) models side by side. Eventually, Halewood will become JLR’s first all-electric production facility, making it a cornerstone of the company’s electrification journey.
“Halewood has been the heart and soul of JLR in the Northwest of England for well over two decades, producing vehicles such as the Range Rover Evoque and Discovery Sport. Halewood will be our first all‑electric production facility, and it is a testament to the brilliant efforts by our teams and suppliers who have worked together to equip the plant with the technology needed to deliver our world class luxury electric vehicles,” said Barbara Bergmeier, Executive Director, Industrial Operations.
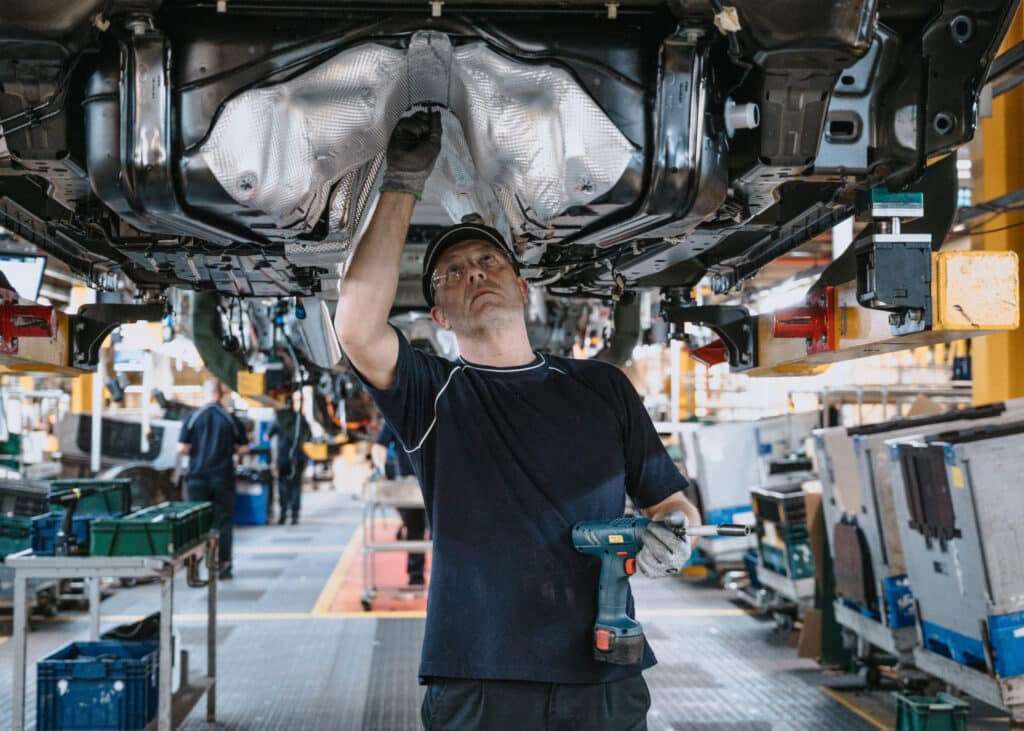
To accommodate the production of different-sized electric vehicles, JLR has undertaken extensive transformational work at its Halewood facility. A new body shop has been built, capable of producing 500 vehicle bodies per day. Additionally, 1.4 km of the paint shop has been modified, including expanded ovens and conveyors, to meet the growing demand for contrasting roofs. A new automated painted body storage tower has been constructed, capable of storing 600 painted vehicle bodies, improving the plant’s efficiency.
The final production line has been extended from 4 km to 6 km to facilitate battery fitment, while vehicle build stations have been lengthened to seven meters to accommodate the varying proportions of the new Electric Modular Architecture (EMA) electric vehicles. To assist employees with the fitment of high-voltage batteries, 40 new Autonomous Mobile Robots (AMRs) have been introduced.
JLR has also prioritized reskilling its workforce for the electric era, delivering High Voltage Training to over 1,600 employees. Furthermore, £16 million worth of equipment from JLR’s Castle Bromwich site, including ABB robots and automated guided vehicles, has been integrated into the new facility, repurposing viable assets to enhance production capabilities at Halewood.
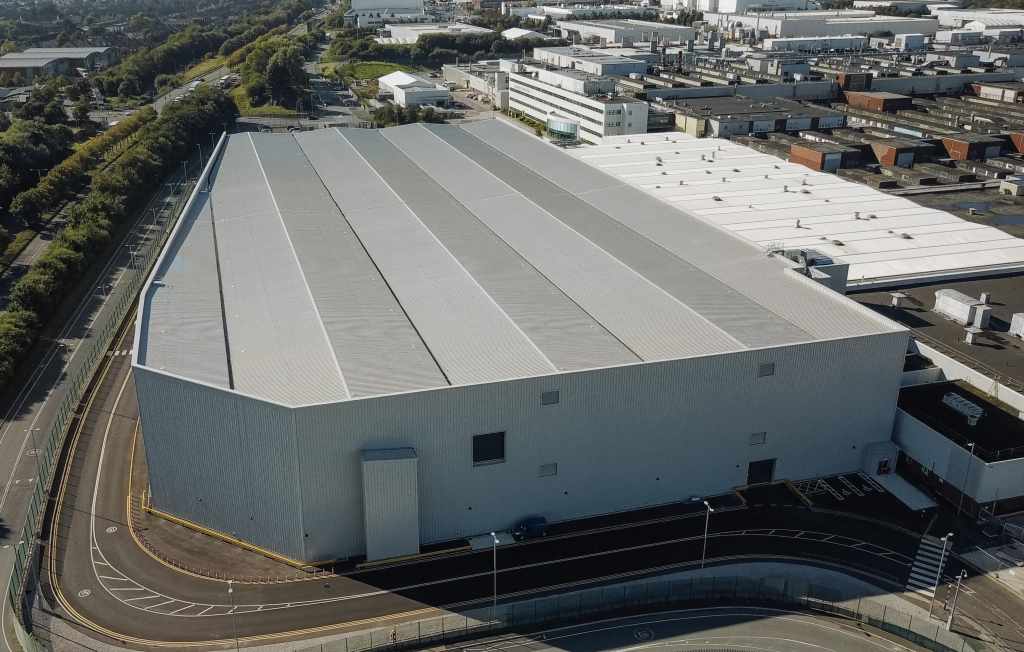
Reimagining Sustainability
As part of its commitment to becoming carbon net zero by 2039, JLR is reimagining sustainability at its Halewood facility by maximizing the use of renewable energy. One significant initiative includes the installation of 18,000 photovoltaic panels, which will generate 8,600 GWh of energy, accounting for 10% of the site’s energy consumption. This renewable energy effort is complemented by a mix of fuel switching and energy efficiency projects, aimed at reducing the facility’s carbon footprint. JLR plans to remove 40,000 tons of CO2e from Halewood’s industrial operations as part of its broader sustainability goals.
Re-skilling Workers for Electrification
To support its transition toward electrification, JLR is heavily investing in employee development through its Future Skills Programme, with £20 million allocated annually across all sites. This investment enables employees to acquire critical skills in new technologies, systems, and processes that are central to the future of automotive manufacturing and engineering.
At Halewood, JLR has opened a new training and development centre, where employees will receive hands-on training with vehicles at various stages of the production cycle. A major focus of the centre is High Voltage Training (HVT), specifically related to battery assembly processes. So far, 1,600 employees have completed HVT, with an additional 100 employees scheduled for training, ensuring that the workforce is prepared for the company’s electrification journey.
A Digital Ecosystem
JLR has introduced new technology at its Halewood facility that automates the fitment of doors to vehicles. Using advanced laser measurement, the system ensures each door is precisely tailored to the body shell, guaranteeing an exceptional quality finish.
As JLR prepares to integrate advanced AI-powered autonomous driving and connected services into its next-generation vehicles, Halewood has also been equipped with new Advanced Driver Assistance System (ADAS) calibration rigs. These rigs are designed to measure the responsiveness of ADAS features, ensuring that each vehicle leaves the facility with the highest level of safety calibration, supporting future autonomous driving capabilities.
With the first test builds of Electric Modular Architecture (EMA) body shells now complete on the new production lines, JLR will continue to test and optimize the new machinery and technology in preparation for the full-scale EMA production.
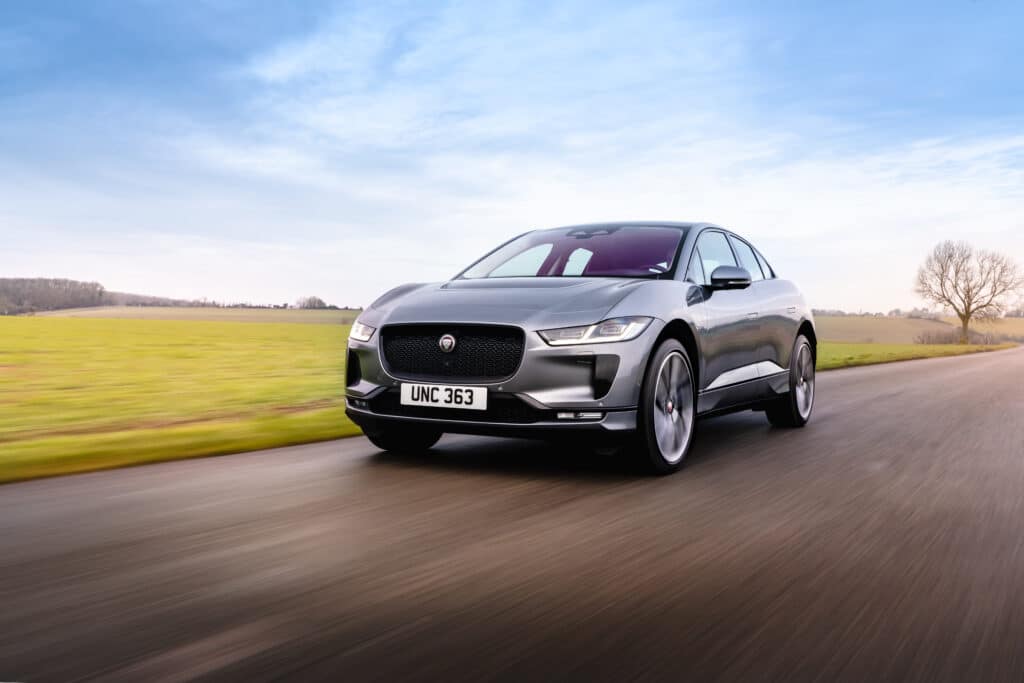
Jaguar and Land Rover Electric Models
The exciting Jaguar I-PACE, Jaguar’s All-electric performance SUV is now available from Jaguar USA. Effortlessly empowered, featuring unyielding acceleration, and capable of 0-100km/h in 4,8 seconds (0-60mph in 4,5 seconds), it is a very impressive vehicle, blowing away competitors.
Jaguar is going all-electric by 2025, with a four-door GT car, an electric SUV and a sedan as part of JLR’s “Reimagine” strategy.
Land Rover is working on an all-electric model and you can join the wait list to potentially be among the first to pre-order the New Range Rover Electric and to receive exclusive updates.

Electric Vehicle Marketing Consultant, Writer and Editor. Publisher EVinfo.net.
Services